Metal Roofing Montana has become increasingly popular due to its durability, longevity, and aesthetic versatility. It is a smart option for homeowners who intend to stay in their homes over the long term.
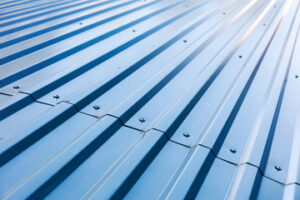
Metal roofs require a little maintenance to ensure they keep their beautiful appearance and extend their lifespan. It is recommended to schedule a professional roof inspection twice per year.
Strength
Metal roofing has been growing in popularity over the last several years as homeowners discover its durability and longevity. If you’re considering this option for your new construction or replacement roof, understanding metal roofing basics will help you make the right choice. This beginner’s guide to metal roofing covers everything from material selection to installation and maintenance tips.
The most popular metal roofing materials are steel and aluminum. Both are highly durable and come in a variety of gauges and finishes. Both materials are extremely versatile and work well in all climates. For example, steel roofing is rust-resistant and can be used in flat or standing seam applications. Aluminum is lightweight and works well in coastal areas and humid environments.
A metal roof can be made to look like almost any other roofing style, including traditional shingles, ceramic tile, and wood shakes. It’s important to choose a roofing style that complements your home’s architecture and reflects your taste.
You can also choose whether to have the fastener panels hidden or exposed, and you can customize your metal roof with different colors, textures, and coatings. You can even have your roof designed to resemble cedar shakes or stone.
A metal roof can increase your home’s resale value by up to 6 percent, and it will help cut energy costs by reflecting sunlight and reducing air conditioning use. However, like any roof, a metal roof requires regular maintenance and inspection to ensure that it’s performing at its best. This includes cleaning, debris removal, and ensuring that gutters and drains are clear of build-up. It’s also important to inspect your roof for signs of damage, such as scuffs, scratches, and dents.
Durability
Metal roofs are known for outliving their asphalt shingle counterparts, with lifespans between 40-70 years. Additionally, their durability and energy efficiency help save homeowners money on heating and cooling costs. With a variety of finishes available, metal roofs can be customized to complement the architecture of any home.
Metal roofing is also more environmentally friendly than other roofing materials, as it can be recycled and reused without losing its strength or quality. Additionally, it resists corrosion, rust, mold, mildew, and pests. Its longevity helps protect underlying structural materials, as well as other exterior features like siding and brick.
Another benefit of metal roofing is its resistance to heavy rain, snow, and high winds compared to other roof types. However, it is important to have the correct insulation and ventilation in place to keep your home comfortable year-round.
When installing a metal roof, it is important to have the proper tools and equipment. For example, you will need an impact gun to install fasteners on the panels. Also, it is essential to check the weather forecast before starting to ensure a dry installation.
When it comes to maintenance, regular inspections can help prevent problems. Keeping the gutters clean can prevent water runoff and debris buildup. In addition, it is a good idea to trim nearby trees to avoid damaging the metal. Inspect the roof regularly for dents, scratches, and fading, and repair any damage immediately. It is also recommended to wash the roof with soapy water twice a year to prevent streaking and to remove dirt and grime that could lead to stains. Finally, it is a good idea to have a warranty on your new metal roof to help cover any repairs that may be needed in the future.
Style
When people first think of metal roofs, they may picture the classic metal roofing seen on barns and sheds. However, today’s homeowners can choose from a wide array of styles, including those that mimic the appearance of traditional shingles, cedar shake, slate, and tile. This gives homeowners a lot of choices and allows them to find a metal roof that perfectly fits their home’s style.
A metal roof’s strength and durability also help cut the cost of maintenance and energy costs. It can withstand high winds, blunt impact, and all the precipitation that commonly knocks out asphalt-fiberglass shingles or wood shakes. It can even be a good choice in areas with frequent hail storms, as long as it has a Class 4 rating, which means it will resist denting, tearing, and other damage caused by large hailstones.
In addition to its weather resistance, a metal roof offers a great deal of insulation and can deflect the sun’s harmful UV rays. This reduces a home’s energy bill and keeps the occupants comfortable throughout the year.
In terms of maintenance, a metal roof is fairly easy to keep clean and in good condition. Regular inspections should be done, and any issues addressed promptly to avoid further problems. For instance, if there’s snow buildup on the roof, it can be swept off using a long-handled broom or brush. You should also trim nearby tree branches, to prevent them from scratching the surface of the roof. Regular cleaning is also a must, to prevent dirt from building up and causing further damage.
Reliability
When homeowners invest in metal roofing, they are making a long-term decision that will benefit them for decades to come. Metal roofs offer durability, longevity, energy efficiency, and low maintenance requirements. When they are installed properly by a professional and maintained regularly with regular inspections, a residential metal roof can last 25 to 50 years or more.
In addition to a long lifespan, a metal roof will also provide better insulation than traditional shingles, helping to cut down on energy costs. And, a light-colored metal roof can help to deflect the sun’s harmful UV rays, further saving money on cooling bills.
A metal roof can also withstand the impact of hail better than a shingle or other material roof. In areas where hail is common, look for a metal roof with a Class 4 impact rating or higher. This will mean that the roof has passed UL’s most severe impact test by withstanding a 2-inch diameter steel ball dropped from 20 feet without tearing, fracturing, or splitting.
A professional should be hired to install a new metal roof. While sinking screws may not seem like a complex task, this type of roofing requires skill and expertise to ensure it is watertight. When selecting a professional, search for one who specializes in the style of metal roof you are interested in. And, be sure to ask for references. To keep track of cutting lines and panel overlaps, use a permanent marker. Don’t use a pencil, as the graphite can degrade metal surfaces. Lastly, trim nearby tree branches to avoid damaging the roof’s surface. Schedule professional inspections every year to check for scuffs, scratches, flaking, or chipping and to address any leaking issues.
Warranty
Metal roofing is a smart investment for homeowners, especially when you consider that it outlasts asphalt-fiberglass shingles and cedar shakes by three to four times. It also provides valuable energy savings. Some insurance companies provide discounts for homes that have a metal roof installed.
A metal roof also offers excellent value because it typically carries a manufacturer’s warranty as well as a service warranty from your roofing contractor. Many of these warranties extend for 30 to 50 years. These warranties are transferable if you sell your home, which adds value to your property and provides peace of mind for the buyer.
The upfront cost of a metal roof can be more than that of other types of roofing, but the investment pays for itself over time. The durability and longevity of a metal roof can protect your home from the elements, reduce energy costs, and increase its resale value. Additionally, the high fire resistance of metal can lower your San Antonio homeowner’s insurance costs.
Some people have preconceived notions about metal roofs that aren’t entirely accurate. For example, they may believe that a metal roof is noisy in the rain or that it will attract lightning. In reality, metal roofs are not noisy in the rain and can be quieter than other types of roofing materials.
However, it’s important to hire a qualified roofer for installation and regular maintenance of metal roofing. A qualified roofer will be familiar with the different products and can offer a quality job at a reasonable price. He or she will also be able to address any concerns you have about the process. When it comes to maintenance, it’s best to clean your metal roof at least once a year to remove any built-up debris such as moss, fungus, or bird droppings. It’s also a good idea to trim nearby tree branches that can scratch the surface of your metal roof.